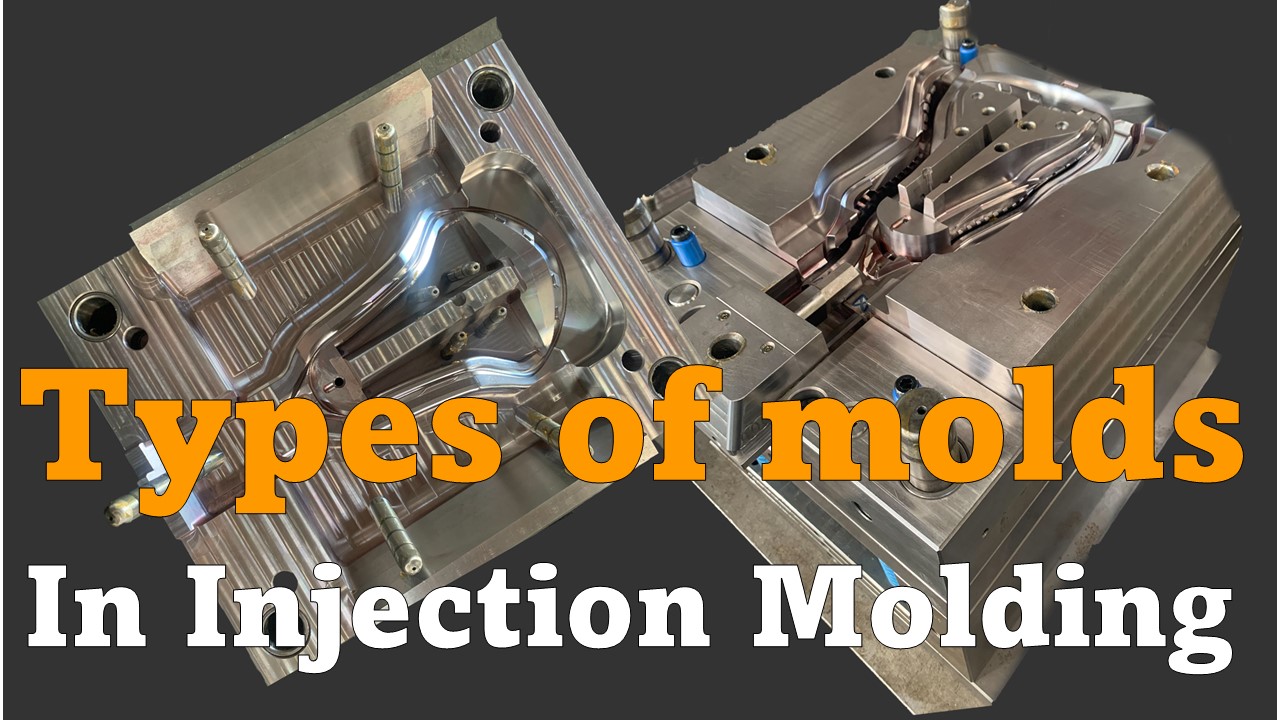
Injection mold type(1) Classification
The Importance of the Right Mold
Choosing the correct mold type for your production is crucial because the type of mold will directly impact product quality, production speed, and, as a result, overall costs. While the type of mold you choose will also influence upfront cost of the mold, it is important to consider that the cost will change if more complexity or stronger tool material is required, such as side actions or pick-outs, or the mold is to be used for overmolding or insert molding.
There are multiple different ways to classify a mold based on different attributes of the mold. Below, we'll discuss the primary two categories:
Type by Runner
The first category of types of injection molds classifies a mold by its type of runner system. A runner system is a series of channels, including a gate, sprue, and runners, that direct the molten plastic material from the machine's nozzle to the desired areas of the mold's cavity.
Hot Runner
A hot runner system involves runners that are either internally or externally heated by rods, coils, or other heating elements. Because it must be heated while the mold is cooled, this type of runner system is encased within a stationary manifold plate. Since the runners are held permanently within this plate, they will not eject with the part, so the molded part comes out clean and devoid of extra plastic waste attached. This reduces waste, and there are no added production steps to remove the runners and recycle them as there are with cold runner systems, meaning production is allowed to move much more quickly. This type of mold is typically used for large volume productions with multiple mold cavities because it is expensive to heat and requires more maintenance that its cold runner sibling. Additionally, because the runners are hidden, it can be difficult to ensure the runners are clean and clear of leftover plastic from previous productions. This can be a disadvantage especially if you are changing material or color between batches. Finally, internally heated hot runner systems can cause problems, such as sticking, when dealing with thermal sensitive materials.
Cold Runner
A cold runner system uses unheated runners to deliver melted plastic into the mold cavity. However, as opposed to hot runners, a cold runner system is exposed because it is cut into the mold itself. This means that a new runner system is made, solidified, and ejected with each mold cycle. Depending on whether a two-plate or three-plate mold is used, the runner system and the molded part may be conjoined or separated when the part is ejected. This type of runner system does create a lot of waste each cycle, but it is simple to grind up the discarded runners to recycle and reuse them. Unfortunately, this adds steps to your production process, so production may be lengthened by this. It is important to note that cold runner systems are easier to clean and maintain for simple color and material changing. Additionally, design changes are easier to incorporate because runner and gate positions can be changed faster than those of a hot runner system. Where internally heated hot runners may struggle with some materials, cold runners work with a wider selection of materials.
Cold runner plate type: two-plate mold, three-plate mold
Another category in injection molds can be classified is the number of their plates. The mold is composed of plates.
When the molds are clamped and pressed together in the injection machine, these plates form a complete finished mold cavity to produce parts.
Two-plate mold
The two-plate mold is the most common type used for injection molding because it has the lowest manufacturing cost. It has only one parting line on which the two halves of the cavity plate intersect. Although both types of runner systems are used in double-plate molds, the cold runner system will still be ejected along with the finished product and will still be attached to the part. More production steps and labor costs are required, and each runner system must be manually dismantled and recycled.
Three-plate mold
The three-plate mold has an additional plate, so that the mold has two parting lines instead of one. The additional plate (stripping plate) is located between the fixed mold and fixed mold installation plate, and is for automatically separate the cold runner system from the molded part during demolding. There is no need to manually cut the runner system and recycle it, which can achieve faster production. Of course, adding a stripper will increase the overall cost of the mold.
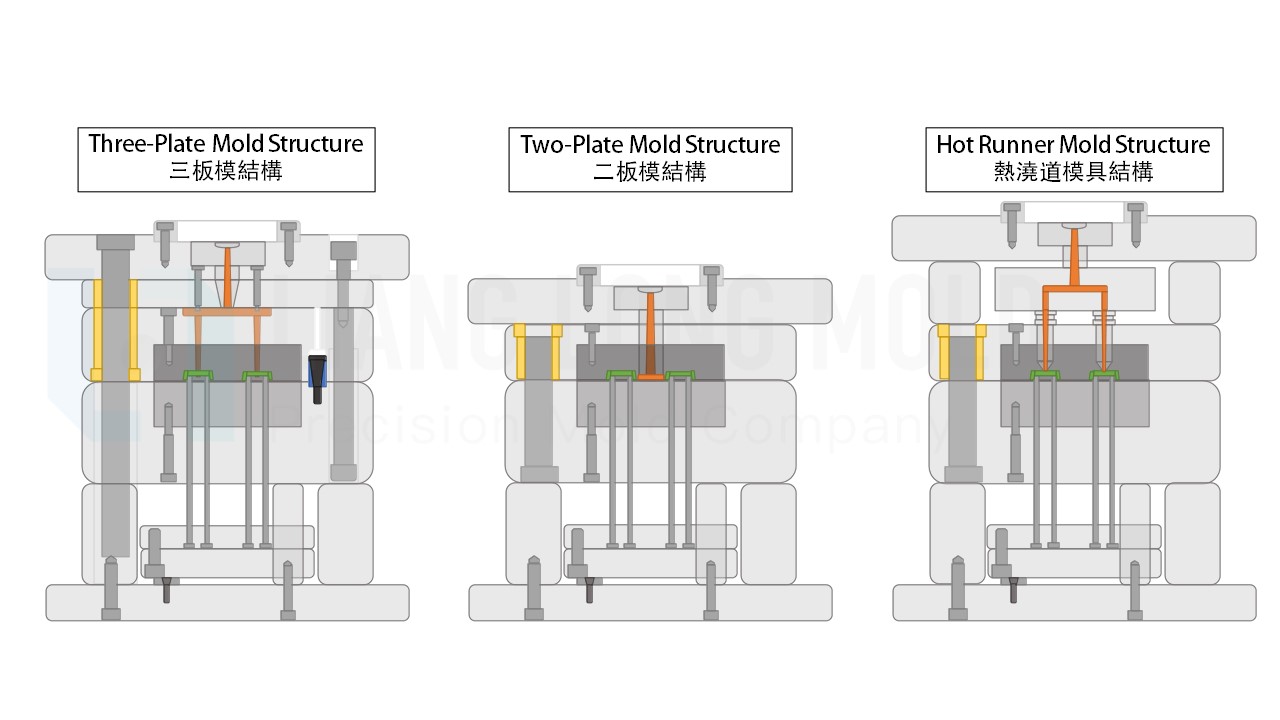