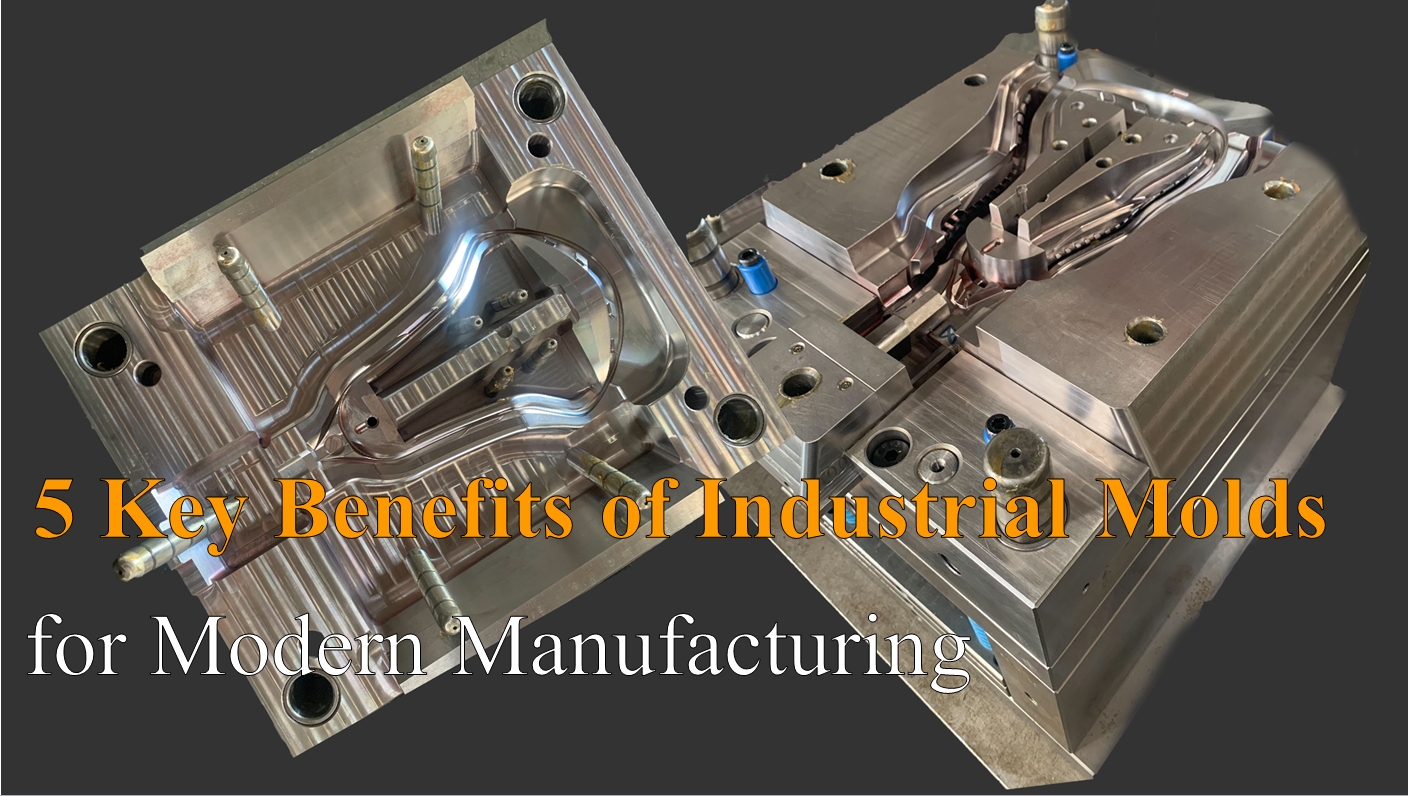
5 Key Benefits of Industrial Molds for Modern Manufacturing
Introduction
Industrial molds are critical to modern manufacturing, providing precision and efficiency across industries like automotive, aerospace, medical, and consumer goods. At Liang Rong Co., Ltd., we focus on delivering high-quality, custom molds for diverse applications. This article explores five key benefits of industrial molds and how they enhance production capabilities.
1. Precision and Consistency
One of the most significant advantages of industrial molds is their ability to consistently produce parts with high precision. Advanced technologies such as CNC machining and precision surface treatments enable molds to maintain tight tolerances, ensuring that every part produced is uniform and meets the strictest quality standards. This is especially important for industries like medical devices and aerospace, where accuracy is critical for performance and safety.
2. Efficiency in High-Volume Production
Industrial molds are designed for rapid production, allowing manufacturers to produce high volumes of parts at fast cycle times. Whether for injection molding, compression molding, or casting, the ability to reuse molds with little to no retooling drastically improves production efficiency. This makes them particularly suited for mass production, where high throughput is required without sacrificing quality.
3. Material Versatility
Industrial molds can be used with a wide range of materials, offering flexibility in terms of product properties. Depending on the application, manufacturers can choose from thermoplastics, rubber, or even metals to achieve the necessary characteristics. For example, high-temperature resistance for engine parts or flexibility for seals and gaskets can be achieved by selecting the right material and mold design. This versatility opens up possibilities for customization, whether for complex geometries or specific material properties.
4. Cost-Effectiveness
While developing an industrial mold may require an initial investment, it is a cost-effective solution in the long run. The ability to reuse molds over numerous production cycles reduces tooling costs. Moreover, the precision of molds minimizes material waste, further driving down production costs. This makes industrial molds an attractive option for businesses producing high-volume parts, especially when looking to improve cost efficiency over time.
5. Customization and Complex Designs
With industrial molds, manufacturers can create highly customized products with intricate designs. Advanced molding techniques allow for the production of parts with detailed features, undercuts, and complex shapes that would be difficult or impossible to achieve using other manufacturing methods. This is particularly valuable in industries that require specialized components, such as automotive interiors, medical devices, and consumer products. Mold customization can also include features like texturing, inserts, or multi-material integration, enabling manufacturers to produce functional and aesthetically pleasing parts.
Innovations in Industrial Molding
n recent years, innovations in mold-making technology have significantly enhanced the capabilities of industrial molds. Techniques such as 3D printing for rapid prototyping and computer-aided design (CAD) allow manufacturers to experiment with mold designs, reducing development time and improving the accuracy of the final product. Additionally, the introduction of smart molds that incorporate sensors for real-time monitoring helps optimize the molding process, resulting in higher efficiency and reduced cycle times.
Applications of Industrial Molds
- Automotive Industry: Producing components like dashboard panels, engine parts, and safety features.
- Consumer Electronics: Manufacturing cases, connectors, and enclosures with precision and reliability.
- Medical Industry: Ensuring safety and hygiene in components like diagnostic devices, surgical tools, and implantable devices.
- Aerospace: Producing lightweight, durable parts that withstand extreme conditions.
Why Liang Rong Co., Ltd. for Industrial Molds?
At Liang Rong Co., Ltd., we stand out as a premier provider of industrial molds due to our extensive expertise and commitment to quality. Our services span from design (DFM) to the development and production of complex molds, including double-package, two-color, and two-material plastic injection, along with insert injection molding. We are equipped with CNC integrated milling and fixture machining capabilities that enhance the precision and efficiency of our production processes. By choosing us, you gain access to a team dedicated to innovation and excellence in mold manufacturing, ensuring that each project meets the highest industry standards and client expectations. Our comprehensive approach and advanced technology allow us to handle projects of any scale and complexity, delivering solutions that drive productivity and success in your operations.
Conclusion
Industrial molds are essential tools for modern manufacturing, offering benefits like precision, efficiency, material versatility, cost-effectiveness, and customization. By investing in high-quality industrial molds, manufacturers can enhance their production capabilities and meet the ever-evolving demands of the market. At Liang Rong Co., Ltd., we are committed to delivering custom mold solutions that drive efficiency, quality, and innovation. Contact us today to learn how we can assist with your industrial mold needs.