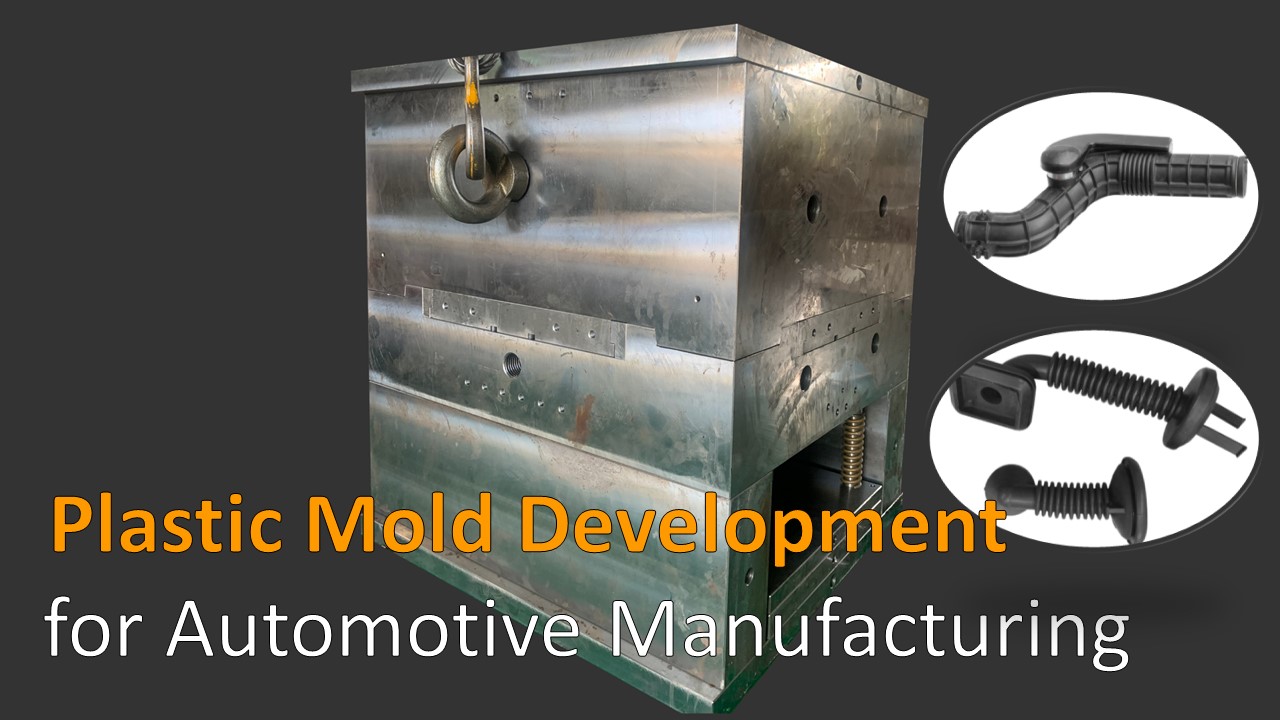
Plastic Mold Development for Automotive Manufacturing
In the automotive industry, collaboration with plastic mold development factories like Liang Rong Co., Ltd. is essential for creating lightweight, durable, and aesthetically pleasing components. We excel in developing critical automotive parts such as Dust Cover Boots, Intake Manifolds, and Automotive Solenoid Valve Parts. Our expertise ensures top-quality manufacturing outcomes across various vehicle segments.
Key Areas for Plastic Mold Collaboration in Vehicle Manufacturing
- Interior Components: These include sophisticated dashboard panels and other cabin features, where aesthetics and functionality merge seamlessly.
- Exterior Parts: We help design and manufacture crucial components like bumpers and mirror casings, optimizing for durability and safety.
- Under-the-Hood Components: Our experience shines in producing parts like intake manifolds and dust cover boots, enhancing vehicle performance and longevity.
- Lighting Components: The precision required for light casings and lenses is achieved through advanced molding processes.
- Electrical Systems: We ensure reliability in the production of connectors and fuse boxes through meticulous mold design.
Technical Considerations in Plastic Mold Manufacturing
When producing automotive parts, several technical considerations must be addressed:
- Material Selection: Different products require specific materials based on their function and placement in the vehicle. For instance:
- Dust Cover Boots: Typically made from durable, flexible materials like thermoplastic elastomers (TPE) to withstand constant flexing and harsh environmental conditions.
- Intake Manifolds: Often crafted from nylon or polypropylene due to their high heat resistance and strength, crucial for components exposed to the engine's thermal environment.
- Automotive Solenoid Valve Parts: Usually use engineering plastics such as polyamide (PA) for its excellent mechanical strength and resistance to heat, ensuring reliability in critical control systems.
- Mold Design and Accuracy: Precision in mold design is not just about dimensional accuracy but also involves ensuring smooth material flow and cooling, which affects the structural integrity and quality of the final product. Advanced CAD software and simulation tools are used to predict and optimize these aspects.
- Thermal Stability: Different components require materials that can not only withstand high temperatures but also maintain their properties over a range of temperatures. For instance, materials for under-hood parts must resist softening at high temperatures, whereas interior components need materials that do not become brittle at lower temperatures.
- Environmental Resistance: Automotive parts need to be resistant to a variety of environmental factors:
- Exterior Components: Materials must withstand UV radiation, moisture, and road salt to prevent degradation and ensure longevity.
- Under-the-Hood Components: Resistance to oils, fuels, and other chemicals is critical to prevent material breakdown and failure.
Conclusion
At Liang Rong Co., Ltd., our commitment to advancing automotive manufacturing through state-of-the-art plastic mold development is unwavering. By leveraging our extensive experience, we continue to provide innovative solutions that enhance vehicle performance and sustainability. For those looking to optimize or develop new automotive components, Liang Rong is your expert partner, ensuring success in both technical and commercial aspects of your projects.