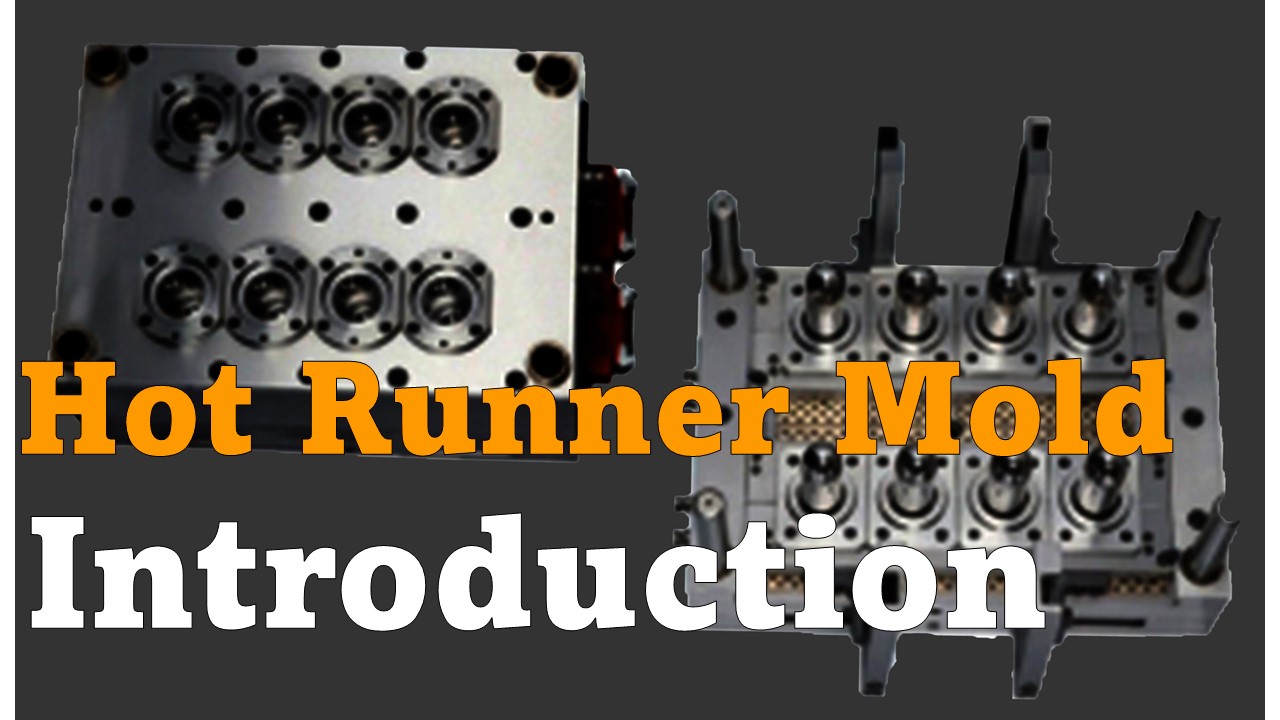
Injection mold type (3) Hot Runner mold
Hot runner
Keeping the plastic in melt state in the sprue and runner at any time during the injection cycle is the hot runner system. Plastic remains in the mold when it is demolded, which is the so-called hot runner injection molding.
Advantage:
*Small gate, small internal stress and good appearance.
*No waste is generated.
*The pressure loss in the runner is small.
*Temperature and pressure of each product are the same,
*The injection pressure can be reduced, and the shrinkage rate can be easily controlled.
*The side gate can be used for forming, single or multiple forming at a time.
Disadvantages:
*High cost of hot runner.
*Not applicable to heat sensitive materials.
*Maintenance and cleaning of hot runner is more difficult than cold runner.
What situation to select hot runner:
1.When forming oversized parts
Using flow length ratio to decide how many hot nozzles should be used to fill the oversized parts totally.
2.Gate locates not at center of the injection machine
If the entry gate cannot be in the center, the length of the runner will be increased to make the plastic flow distance longer. In this condition, the hot runner manifold and nozzle can be applied to improve plastic flow makeit smooth and faster.
3. When gate is required from the movable mold side (eject side) or a long vertical sprue is required:
Let the runner extend directly to the inside of the movable mold for pouring. Because there is no runner will be ejected, so the hot runner can realize the eject side pouring method.
4. Difficult to form parts:
Difficult to form materials (PEEK, PPS, etc.), fiber reinforced materials or thin parts with a thickness of less than 1mm can be solved with hot runners.
5. High cost material price:
If the number of plastic parts exceeds 50 NT dollar per kilogram and the quantity of plastic parts is required to be large, the hot runner system can be carefully considered.
Hot runner selection steps:
(1) Calculate or scale the weight of the product
(2) Determine how many hot nozzles, the weight of the finished product/the number of hot nozzles = the amount of each shot, find the correct specification in the catalogue
(3) Look for the specifications and dimensions of the hot nozzle (for two or more, use a branch runner plate)
(4) Determine the position of the hot nozzle
(5) Determine the position the size and shape of the branch runner plate
(6) Determine the size of the sprue
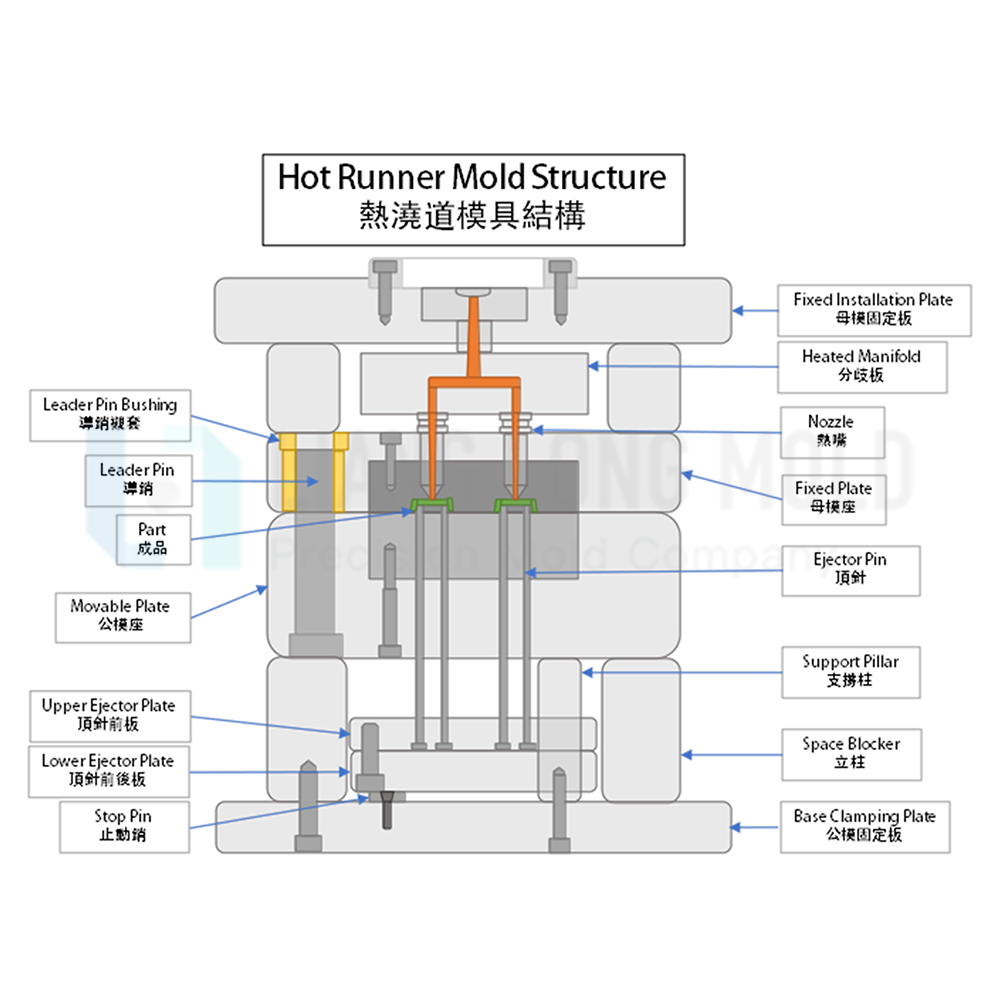