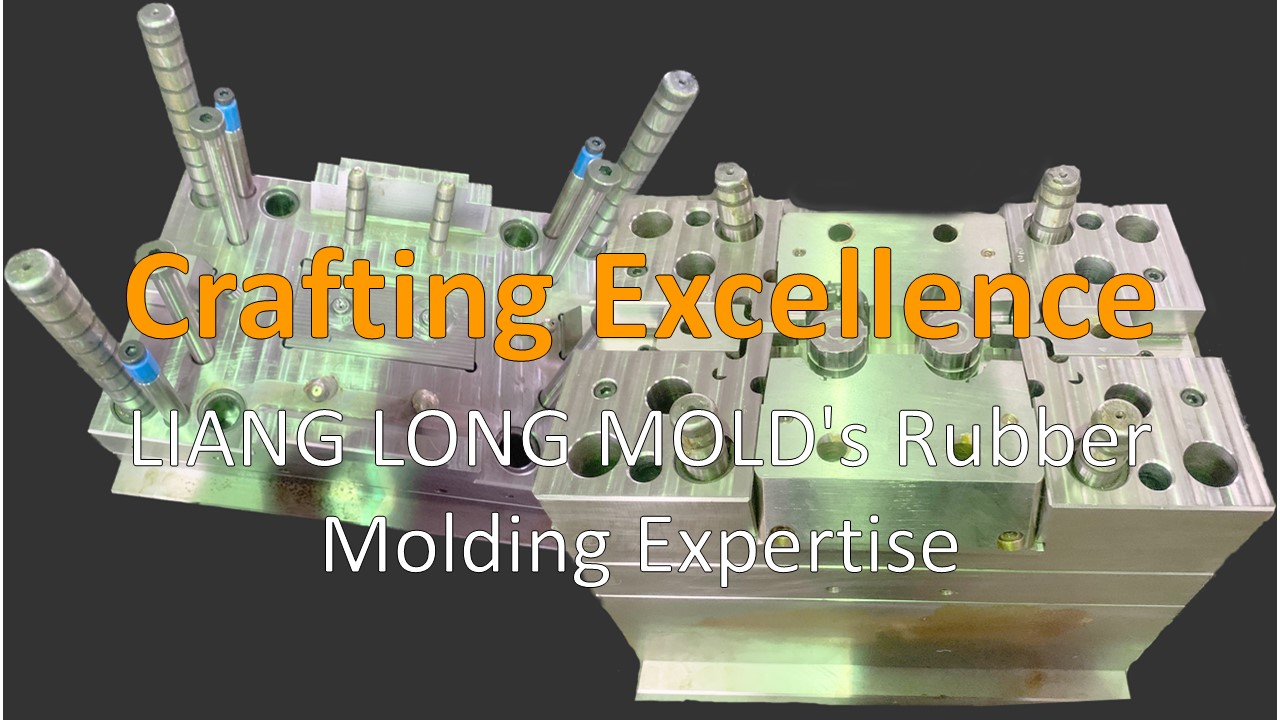
Crafting Excellence: LIANG LONG MOLD's Rubber Molding Expertise
Introduction to Rubber Molding
Rubber molding stands as a cornerstone in the manufacturing world, offering unparalleled flexibility and durability across myriad applications. At LIANG LONG MOLD, we harness this transformative process to turn raw rubber into precision-engineered parts crucial for various industries, including automobile,consumer products and leisure products. This process requires meticulous attention to detail and a deep understanding of material science and engineering principles. Our commitment to excellence in rubber molding is rooted in our dedication to quality, innovation, and fulfilling the unique needs of our clients.
Types of Rubber Molding Processes
The rubber molding process encompasses various techniques, each with its own set of advantages, tailored for specific manufacturing requirements and design intricacies. Here's an overview of the primary types of rubber molding processes:
- Compression Molding: This is a cost-effective and straightforward method used for producing medium to large rubber parts. In this process, preheated rubber material is placed into a heated mold cavity. The mold is then closed and pressure is applied, causing the rubber to conform to the mold's shape as it cures. Compression molding is well-suited for making large, simple-shaped items and is known for its low waste production.
- Transfer Molding: Transfer molding is an advancement over compression molding, designed for creating more complex parts. It begins with placing raw rubber into a portion of the mold called the pot. Once the mold is closed, pressure forces the rubber from the pot through a gate into the cavity of the mold. This method allows for tighter tolerance and more intricate parts compared to compression molding, making it ideal for components requiring precision and detailed features.
- Injection Molding: Injection molding is a highly efficient process used for producing rubber parts with complex shapes and tight tolerances in high volumes. The rubber is first heated until it reaches a molten state and then injected into a closed, heated mold cavity. It solidifies into the final part shape upon cooling. Injection molding is notable for its fast cycle times, repeatability, and the ability to reduce material waste, making it suitable for mass production.
Each of these rubber molding processes offers unique benefits and is chosen based on the specific requirements of the part being manufactured, including its size, complexity, and the production volume needed.
Materials Used in Rubber Molding
Rubber molding is a versatile manufacturing process that can use a variety of materials, each offering unique properties to meet diverse application requirements. Here's an overview of common materials utilized in rubber molding:
- Natural Rubber (NR): Derived from latex, natural rubber has excellent elasticity, tear strength, and tensile strength. It's widely used for products requiring high flexibility and dynamic performance, such as tires, gaskets, and shock absorbers.
- Nitrile Rubber (NBR): Known for its resistance to oil, fuel, and other chemicals, Nitrile Rubber is ideal for automotive and industrial applications where exposure to oils and chemicals is common.
- Silicone Rubber: Exceptional for its high temperature resistance and stability over a wide range of temperatures. Silicone rubber is often chosen for medical devices, kitchenware, and seals in high-temperature environments.
- Ethylene Propylene Diene Monomer (EPDM): EPDM is highly resistant to weathering, ozone, and UV rays, making it suitable for outdoor applications such as roofing materials, window seals, and waterproofing sheets.
- Fluorocarbon Rubber (Viton): Offers excellent chemical resistance, high temperature tolerance, and durability in aggressive chemical environments. It's often used in the aerospace, automotive, and chemical processing industries for seals and gaskets.
- Styrene-Butadiene Rubber (SBR): A synthetic rubber that provides good abrasion resistance and is used in a variety of applications, including automotive tires, conveyor belts, and various industrial goods.
- Butyl Rubber (IIR): Known for its low permeability to gases and high resistance to heat, chemicals, and oxidation. Butyl rubber is commonly used in inner tubes, pharmaceutical stoppers, and protective clothing.
Each material brings distinct advantages to the molding process, allowing for the creation of products tailored to specific operational conditions and performance requirements. The choice of material depends on factors such as the desired properties of the final product, the environment it will be used in, and cost considerations.
Showcasing Mastery: LIANG LONG MOLD's Rubber Molding Achievements
Reflecting our deep commitment to innovation and quality in rubber molding, we are proud to share a selection of case studies that showcase our expertise and creative solutions to complex challenges:
- Automotive Mastery: Our expertise shines in the automotive sector, where we've engineered high-precision parts like Dust Cover Boots and Automotive Solenoid Valve Parts. These components underscore our capability to produce parts that meet stringent automotive standards, enhancing vehicle reliability and performance.
- Everyday Solutions: We've also focused on improving daily life with the development of versatile products like rubber sheaths. These items showcase our commitment to enhancing everyday convenience and safety, emphasizing our dedication to quality and practical innovation.
These case studies exemplify the essence of LIANG LONG MOLD's commitment to excellence in rubber molding. Through our innovative approach and relentless pursuit of quality, we have successfully tackled diverse challenges, affirming our position as industry leaders. Our journey is a testament to our expertise, creativity, and the unwavering dedication to meeting our clients' needs.
Conclusion
Rubber molding, a synthesis of art and science, requires in-depth material knowledge and engineering innovation to solve industry-wide challenges. At LIANG LONG MOLD, we are proud of our comprehensive industry understanding, state-of-the-art techniques, and steadfast commitment to excellence. Whether addressing needs in the automotive, medical, or any other field, we are dedicated to bringing our clients' visions to life with top-tier rubber molding solutions, backed by our extensive product range and mold development capabilities.
For collaborations, inquiries, or to learn more about how we can elevate your project, contact us. Together, let's shape the next generation of rubber molding solutions, where your visions become reality with LIANG LONG MOLD's signature precision and excellence.